What are the characteristics of this specific group of gyroscopic devices? Understanding the design principles and variations within this family is crucial for selecting the appropriate tool for a given application.
This group likely refers to a classification of gyroscopes, categorized based on shared design features. These features might include the type of rotor, the method of sensing angular velocity, the materials used in construction, or the overall architecture. For example, the family could encompass various gyroscope types, such as ring laser gyros, fiber optic gyros, or MEMS (micro-electromechanical systems) gyroscopes. Each type might exhibit unique performance characteristics, including precision, sensitivity, and cost, thus making it essential to understand the distinctions within the group.
Understanding the specific gyro family provides critical insight into its capabilities and limitations. This knowledge is paramount in engineering and scientific applications requiring precise angular measurement. The development of new types within this family often leads to improved performance in areas such as navigation, aerospace engineering, and robotics. Historical context might highlight the evolution of gyroscopic technology within this particular group, tracing advancements in materials, manufacturing processes, and sensor technologies. This, in turn, provides a richer appreciation for the present state of the technology.
- Captivating Lee Yool A Guide To The Stars Life And Career
- A Comprehensive Guide To Axl Roses Age Unraveling The Mysteries
Moving forward, the article will delve deeper into the practical applications and specific characteristics of these gyroscopic devices, illustrating the importance of categorization in the field of engineering and scientific research.
Gyro Zepelii Family
Understanding the "Gyro Zepelii Family" requires examining its defining characteristics and applications. This family likely encompasses a specific group of gyroscopic devices, distinguished by shared design principles.
- Design Features
- Performance Metrics
- Application Domains
- Technological Advancements
- Manufacturing Processes
- Cost Considerations
These aspects, such as design features (rotor type, sensor mechanisms), performance metrics (precision, sensitivity), and application domains (navigation, robotics), collectively define the "Gyro Zepelii Family." Technological advancements and manufacturing processes influence cost considerations, affecting the viability of diverse applications. For example, improvements in micro-manufacturing have enabled the development of more compact and affordable gyros, expanding their usage in consumer electronics. Understanding these interconnected aspects is crucial for evaluating the suitability of a particular gyro for a specific task.
1. Design Features
Design features are fundamental to the "Gyro Zepelii Family," dictating performance characteristics and suitability for specific applications. Identifying key design elements provides insight into the capabilities and limitations of each member within this family of gyroscopic devices. Understanding these features is essential for selecting the appropriate device for a given task.
- Rotor Type and Construction
The type of rotor and its construction significantly influence the gyro's sensitivity, responsiveness, and stability. Different rotor materials, shapes, and mounting methods contribute to varying degrees of precision and robustness. For example, a lightweight, precisely balanced rotor might be crucial for high-speed applications, while a more robust design might be necessary for harsh environments. These choices are directly related to the performance capabilities expected from a given device within the "Gyro Zepelii Family."
- Sensing Mechanism
The method by which the device senses angular velocity is crucial. Different sensing mechanisms, such as those employing optical fibers, lasers, or MEMS technology, yield various levels of accuracy and responsiveness. The choice of sensing method directly impacts the device's overall performance and cost, factors that contribute to defining a particular device's place within the "Gyro Zepelii Family." Consider, for instance, the tradeoffs between precision and cost associated with different sensing technologies.
- Packaging and Mounting
Packaging and mounting methods influence the gyro's susceptibility to environmental factors and its ability to integrate into larger systems. A robust packaging design protects the sensitive components from vibrations, shocks, and temperature fluctuations. Suitable mounting configurations facilitate secure integration into diverse systems and applications. Thus, packaging and mounting designs play a critical role in determining a gyro's overall reliability and suitability within the "Gyro Zepelii Family."
- Calibration Techniques
Calibration procedures impact the accuracy and consistency of measurements. Effective calibration ensures the gyro's readings accurately reflect the actual angular velocity. This element is vital in applications demanding high precision, such as inertial navigation systems. Proper calibration procedures are directly correlated to the performance expectations of gyros within the "Gyro Zepelii Family," thus influencing their usability in various domains.
These interconnected design features determine the capabilities and applicability of various gyroscopes within the "Gyro Zepelii Family." By analyzing these components, one gains a deeper understanding of the technical choices that define each device and its appropriateness for specific tasks. Comparative analysis of different design features is necessary to effectively discern the specific advantages and disadvantages of each member in the family.
2. Performance Metrics
Performance metrics are integral to the "Gyro Zepelii Family." They define the capabilities and limitations of each gyroscope within the classification. These metrics directly influence the suitability of a gyro for specific applications. Accuracy, precision, and sensitivity, for example, are crucial in inertial navigation systems where slight errors can lead to significant miscalculations. Reliability, measured in terms of stability and drift, is paramount in applications demanding consistent performance, such as aerospace guidance systems.
Consider the differing performance metrics across diverse members of the "Gyro Zepelii Family." A gyroscope designed for high-precision applications, such as those in aircraft navigation, will prioritize accuracy and stability. Conversely, a system intended for low-cost consumer devices might prioritize lower cost by accepting lower accuracy. The trade-offs between these performance metrics are crucial in choosing the appropriate gyroscope for any given application. Real-world examples include the gyroscopes employed in high-end racing cars, demanding exceptional precision for handling, and those in consumer-grade gaming peripherals where a balance of price and responsiveness is paramount. Understanding these variations and their implications is fundamental to effectively employing gyroscopes.
In summary, performance metrics are crucial determinants in the context of the "Gyro Zepelii Family." They underpin the selection process, dictate suitability for specific tasks, and provide a benchmark for evaluating and comparing different gyroscopes. The specific performance characteristics of a particular device directly impact its applicability within various applications, ranging from sophisticated aerospace systems to everyday consumer electronics. Understanding and quantifying these metrics is crucial for ensuring the appropriate application of the chosen gyro within the relevant domain.
3. Application Domains
The "Gyro Zepelii Family," as a classification of gyroscopic devices, is inextricably linked to its application domains. The specific design features and performance metrics of each device within the family dictate its suitability for particular tasks. A crucial aspect of understanding this family is recognizing how the design choices directly impact functionality in real-world scenarios. For instance, gyroscopes designed for high-precision navigation in aerospace applications differ significantly from those intended for consumer-grade gaming peripherals, reflecting the varied demands of each domain. The selection of a specific gyro is profoundly influenced by the performance requirements of its intended use. Navigation systems in aircraft demand gyros with exceptional accuracy and stability, while gaming controllers might prioritize low cost and responsiveness. This cause-and-effect relationship highlights the critical role of application domains in defining the characteristics and utility of gyroscopes.
The application domains themselves range widely, encompassing diverse fields. In aerospace, gyroscopes are fundamental to inertial navigation systems, enabling accurate aircraft positioning and guidance. In robotics, gyroscopes contribute to stability and precise movement control, enabling intricate tasks and navigation. Consumer electronics frequently incorporate gyroscopes for motion sensing in applications like smartphones and gaming devices. Furthermore, the automotive industry employs gyroscopes for stability control systems, such as anti-lock braking systems and electronic stability control. These examples illustrate the breadth and depth of applicability for this family of gyroscopes, emphasizing the diverse design requirements associated with various application contexts.
Understanding the correlation between the "Gyro Zepelii Family" and its application domains is crucial for selecting the appropriate gyroscope for a particular need. Failure to account for specific demands within a given application domain can result in suboptimal performance, inaccuracies, or even system failure. Therefore, meticulous consideration of application requirements is paramount in the design and selection process. Furthermore, the development of new gyroscopic technologies often stems from the requirements of novel application domains, creating a continuous cycle of innovation and adaptation. Consequently, the connection between the "Gyro Zepelii Family" and its diverse application domains is not static but rather dynamically evolving as new applications emerge and technologies advance.
4. Technological Advancements
Technological advancements are intrinsically linked to the evolution of the "Gyro Zepelii Family." Improvements in materials science, manufacturing processes, and sensor technologies directly influence the design, performance, and cost-effectiveness of gyroscopic devices. Advancements in micro-fabrication techniques, for example, have enabled the creation of miniature gyroscopes, crucial for integration into compact devices like smartphones and wearable technology. Parallel developments in sensor technology have improved the accuracy and reliability of measurements. The ability to miniaturize components while simultaneously increasing precision is crucial for expanding the applications of gyroscopic devices. Consequently, technological progress fuels the innovation within this family.
Consider the impact of laser technology. The development of laser gyroscopes, for instance, significantly enhanced the precision and stability of angular measurement compared to earlier mechanical gyros. This advancement was pivotal in enhancing navigation systems, enabling more precise and reliable guidance in aerospace applications. Similarly, the refinement of microelectromechanical systems (MEMS) technology has led to the creation of cost-effective and compact gyroscopes for consumer electronics. These advancements exemplify the direct correlation between technological progress and the development and improvement of gyroscopic devices, resulting in diverse and expanded applications.
In summary, technological advancements are a fundamental driving force behind the evolution of the "Gyro Zepelii Family." These advancements enable enhancements in performance, reduce costs, and open up new possibilities for application. Understanding the interplay between technological progress and the development of gyroscopes is crucial for predicting future trends, identifying potential limitations, and recognizing the critical role technological evolution plays in shaping the usability and applications of this technology. Without continuous technological innovation, the "Gyro Zepelii Family" would likely stagnate, limiting its applicability and impact across diverse fields.
5. Manufacturing Processes
Manufacturing processes directly impact the characteristics and capabilities of gyroscopic devices within the "Gyro Zepelii Family." The methods employed in creating these components influence cost, precision, and ultimately, the suitability of the device for its intended application. Different manufacturing techniques are tailored to the specific design parameters and performance requirements of each member of this family.
- Material Selection and Processing
The choice of materials and their subsequent processing are fundamental. For instance, high-precision gyroscopes often utilize specialized alloys exhibiting low thermal expansion and high strength. The precision in material processing dictates the uniformity and quality of the gyro's components, influencing overall accuracy. Different manufacturing techniques, such as casting, machining, and additive manufacturing (3D printing), affect the final material properties and tolerances. These choices directly correlate to the cost and performance of the resulting device, ultimately affecting its placement within the "Gyro Zepelii Family."
- Precision Machining and Assembly
Precise machining ensures accurate component dimensions, crucial for achieving high-level precision in gyroscopes. Specialized machinery and skilled labor are often required. For critical components like rotors, tolerances must be exceptionally tight to minimize friction and maximize stability. The assembly processwhether automated or manualcontributes to overall reliability and structural integrity. Errors in precision machining or assembly will directly impact the gyro's performance and thus its placement within the "Gyro Zepelii Family." An inconsistent assembly process might compromise the device's expected accuracy.
- Sensor Integration and Calibration
Integrating sensors, such as those based on laser or MEMS technology, requires specific procedures. The integration process must maintain the sensor's calibration and sensitivity. Sophisticated calibration techniques are critical to ensure consistent and accurate readings, affecting the gyro's overall accuracy. Maintaining the integrity of these integrated sensor systems is vital to ensure the gyro's performance within its specific application domain, thereby contributing to its positioning in the "Gyro Zepelii Family."
- Environmental Controls During Manufacturing
Manufacturing environments play a crucial role. Precise temperature and humidity control are often necessary to maintain stable material properties and reduce errors during production. These environmental considerations are particularly vital for components susceptible to thermal expansion, influencing the overall accuracy of the final product. Maintaining consistent manufacturing conditions is essential for quality control and reproducibility, factors directly relevant to a gyro's placement within the family.
In conclusion, manufacturing processes are intrinsically intertwined with the characteristics and performance of gyroscopes within the "Gyro Zepelii Family." The techniques employed throughout the production process, from initial material selection to final assembly, influence the gyro's accuracy, stability, and ultimately, its applicability in diverse fields. Understanding these intricate relationships is essential for selecting the appropriate manufacturing process for a specific type of gyro, ensuring that the resulting device meets the necessary performance criteria for its designated application domain.
6. Cost Considerations
Cost considerations are inextricably linked to the "Gyro Zepelii Family." The economic factors associated with the design, manufacturing, and application of gyroscopic devices significantly influence their selection and integration into various systems. Understanding these costs is crucial for optimal decision-making in diverse fields, from aerospace engineering to consumer electronics.
- Material Costs and Availability
The cost of materials used in gyro construction is a major factor. Precious metals or specialized alloys for high-precision gyroscopes significantly increase production costs. The availability of these materials can also fluctuate, introducing price volatility and potentially impacting the feasibility of manufacturing certain models. Variations in material costs directly affect the pricing structure of different gyros within the "Gyro Zepelii Family."
- Manufacturing Process Complexity and Scale
Manufacturing complexity influences cost. Gyroscopes requiring intricate machining, specialized assembly, and meticulous calibration procedures often command higher prices. The scale of production plays a role; mass production can decrease unit costs, while specialized, limited-run gyros typically have higher individual costs. Cost-effectiveness within the "Gyro Zepelii Family" is significantly impacted by manufacturing scale and complexity.
- Labor Costs and Expertise
Labor costs, encompassing skilled technicians and engineers involved in design, manufacturing, and quality control, significantly impact the overall cost. The technical proficiency demanded by particular gyroscope designs influences labor costs. Specialized expertise necessary for intricate assembly or calibration processes directly affects pricing. The labor-intensive nature of certain gyroscope production methods leads to higher overall costs, influencing cost-effectiveness within the "Gyro Zepelii Family."
- Sensor Technology and Integration
Different sensor technologies, such as ring laser or MEMS gyros, vary in cost. The integration of advanced sensors into gyroscopic systems can elevate production costs. Design intricacies and the level of integration affect the total cost. Consideration of the price-to-performance ratio of distinct sensor types is critical in selecting the right gyroscope for a given project within the "Gyro Zepelii Family."
Ultimately, cost considerations are essential for evaluating the practicality and competitiveness of gyroscopes within the "Gyro Zepelii Family." Trade-offs between cost and performance are critical when choosing gyroscopes for specific applications. Understanding the interplay between material costs, manufacturing complexities, labor requirements, and sensor technology is paramount in optimizing design and ensuring a cost-effective solution for any project. The specific cost considerations for a given design within the "Gyro Zepelii Family" will directly influence its application and impact on a project.
Frequently Asked Questions
This section addresses common inquiries regarding the Gyro Zepelii family of gyroscopic devices. Questions range from fundamental definitions to more complex technical considerations.
Question 1: What defines the Gyro Zepelii family?
The Gyro Zepelii family likely represents a specific classification of gyroscopic devices characterized by shared design principles. These principles might encompass rotor type, sensing mechanism, materials of construction, and overall architecture. Further specifications are needed for a precise definition.
Question 2: What are the typical applications of these gyroscopes?
Typical applications depend on specific design characteristics within the family. Potential applications could include inertial navigation systems in aerospace, precise motion control in robotics, and motion sensing in consumer electronics. Detailed specifications are necessary to determine appropriate applications.
Question 3: How do the performance metrics of gyros within this family compare?
Performance metrics, such as precision, sensitivity, and reliability, vary among different members of the Gyro Zepelii family. Precision models might prioritize high accuracy for critical applications, while others might focus on cost-effectiveness, compromising on certain precision aspects. Specific technical details are essential to understand comparative performance metrics.
Question 4: What are the technological advancements driving developments within this family?
Technological advancements in materials science, manufacturing processes, and sensor technology are crucial. Miniaturization, enhanced precision, and lower production costs are potential benefits of these advancements. Understanding these technological developments within the context of a particular design is vital.
Question 5: What are the typical cost considerations for these gyroscopes?
Cost considerations depend on specific design features and manufacturing processes. Factors including material costs, manufacturing complexity, and required expertise influence pricing. Detailed design specifications and production volume influence the cost-effectiveness of a particular model within the Gyro Zepelii family.
Understanding the diverse characteristics within the Gyro Zepelii family requires detailed design specifications, performance metrics, and intended applications for each individual device.
The following sections will delve into specific design features, performance metrics, and application domains of the family.
Conclusion
The Gyro Zepelii family represents a diverse group of gyroscopic devices, distinguished by a range of design features, performance characteristics, and application domains. Analysis reveals that critical factors such as rotor type, sensing mechanisms, and manufacturing processes directly influence the capabilities and cost-effectiveness of each member. Precision machining, material selection, and sensor integration are integral aspects contributing to the final product's performance within specific applications, ranging from aerospace navigation to consumer electronics. Understanding these interrelationships is crucial for appropriate selection and integration. Cost considerations, encompassing material costs, manufacturing complexity, and expertise requirements, further shape the viability and practical application of these devices. The evolution of this family is deeply intertwined with technological advancements, notably in sensor technology, materials science, and manufacturing methods, enabling the continuous improvement of performance metrics and cost reduction.
The continued development of the Gyro Zepelii family hinges on future technological advancements and evolving application needs. Continued research and innovation in these areas will likely lead to even more precise, cost-effective, and versatile gyroscopic devices. The ability to predict future applications and tailor design specifications accordingly will be crucial for realizing the full potential of the Gyro Zepelii family and its impact on various fields. Further exploration into specific design parameters and performance metrics of individual members within the Gyro Zepelii family is warranted for a more comprehensive understanding of their capabilities and limitations.
- Unlock The Power Of Jackerman A Comprehensive Guide To Mastering The Art
- Pioneer Womans Colon Cancer Journey Stage 4 And Beyond
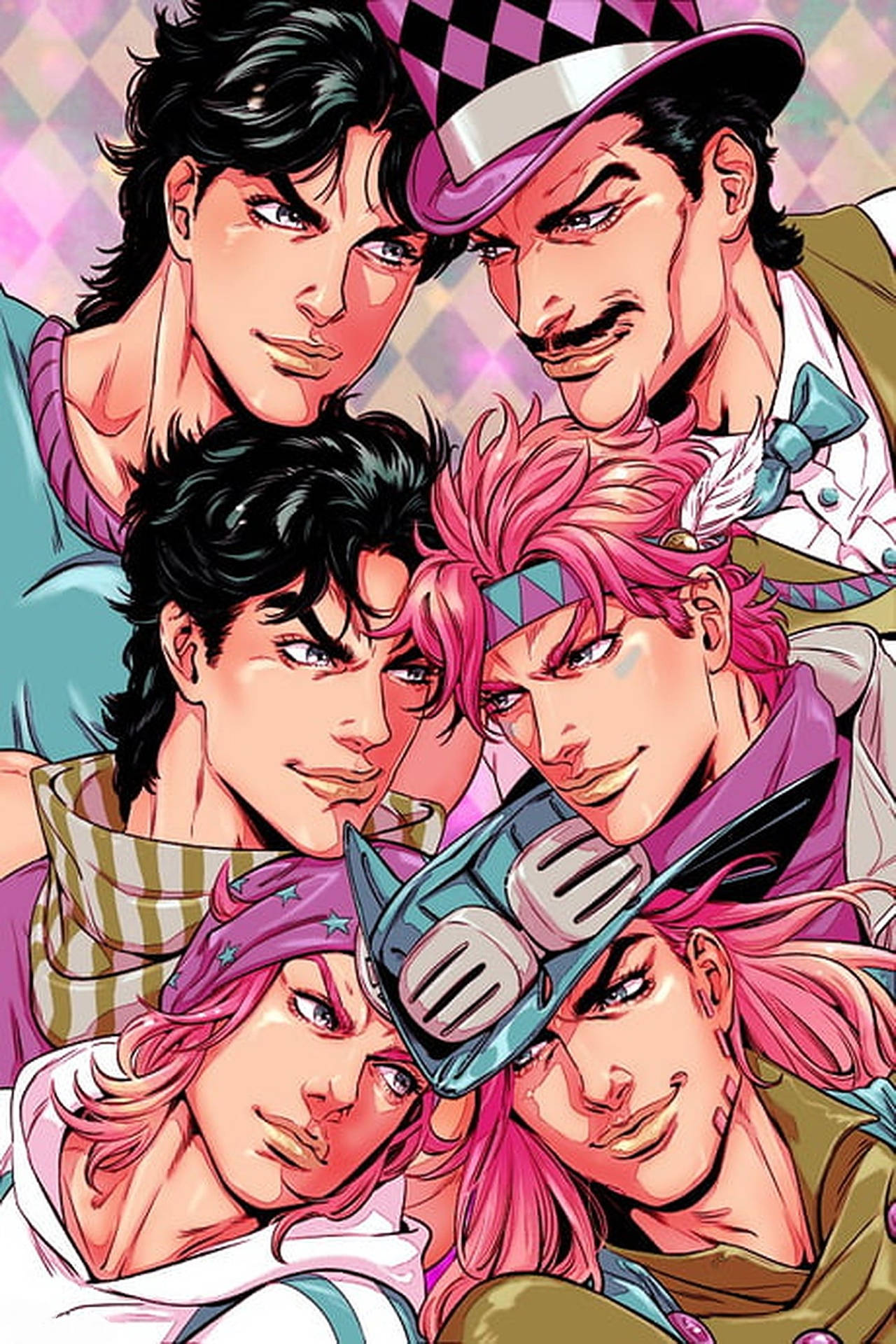
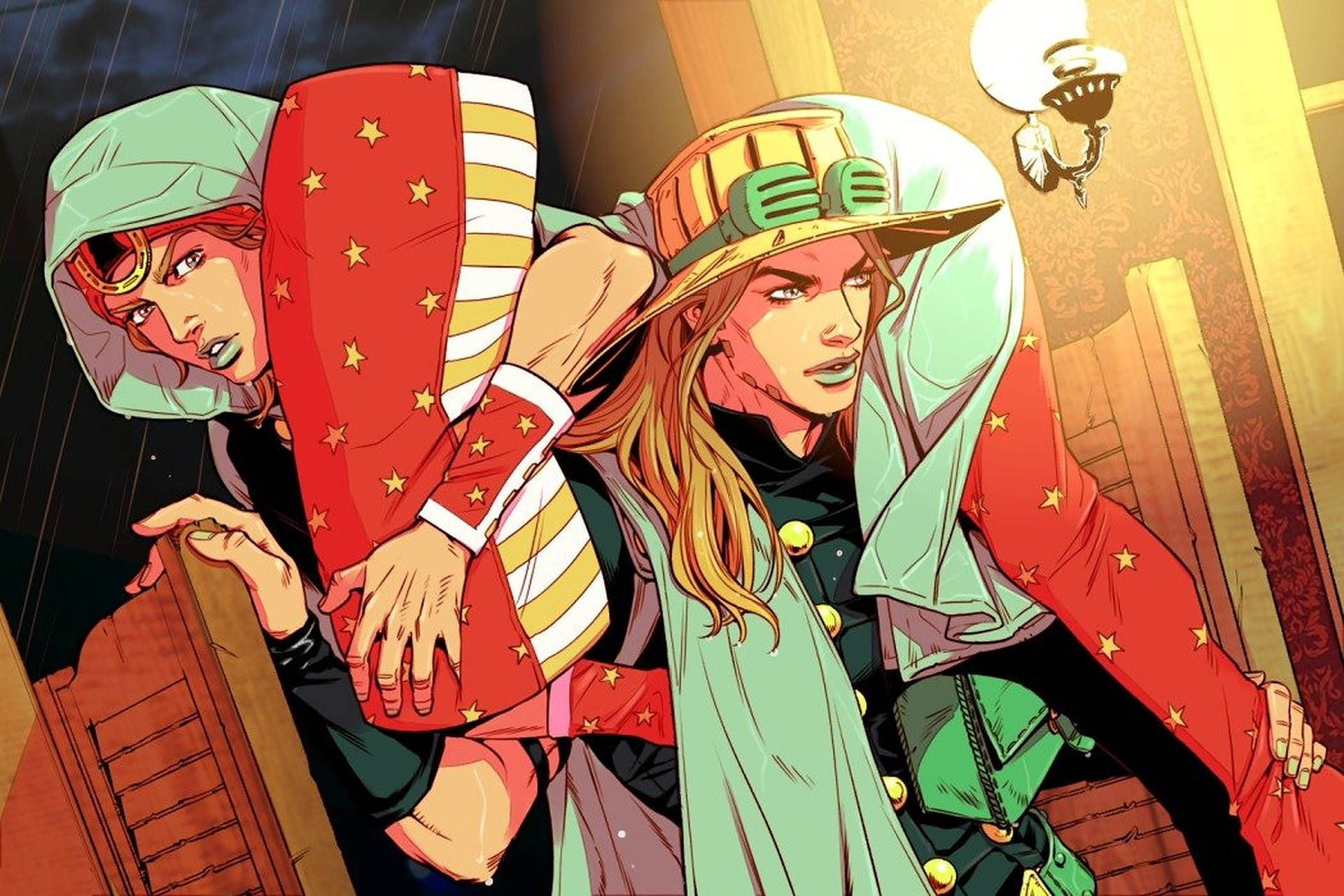
